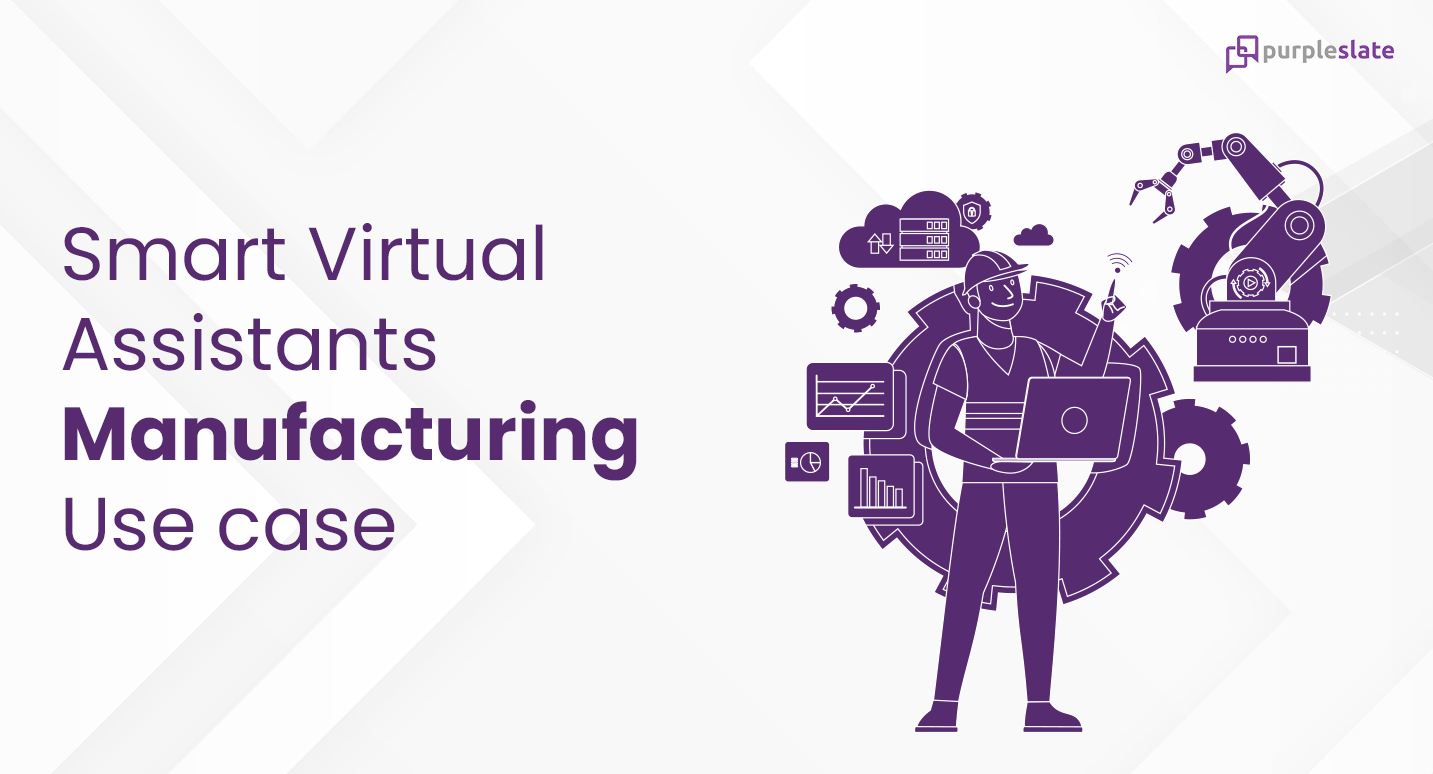
Introduction
Interpersonal skills – The term both managers and HR use quite often when they talk about team cohesion, team management and leadership traits. Now it is getting replaced with fusion skills. Fusion skills? What is it? Is it related to music where the classical meets the pop? Not exactly, but somewhere near that. Still, confusing? It is a distinctive human skill to work effectively with Artificial Intelligence systems. AI is here to stay and humans have to collaborate with AI systems to be relevant in the workforce.
Some things are natural to humans (emotions like laughing, and crying) and some things are easier for AI (repetitive tasks, analyzing Zeta bytes of data). In the current ecosystem, any business requires both of these capabilities. The right combination of humans and AI will take the business to the next level in supersonic speed. Is there a formula or time-tested ratio for this combo? Well, it varies and depends on the business vertical and operations it is implemented. Companies must understand how humans can most effectively augment AI, how AI can enhance what humans do best and accordingly redesign the business processes.
The general (mis)conception is AI is used only in customer support or repetitive tasks that don’t require human intervention. AI has come a long way and one of its critical implementations, Conversational AI (CAI) is breaking its barrier across conservative business verticals like Manufacturing industries. Chatbots and Smart Assistants are the two famous CAI implementations. McKinsey had forecasted that Smart Virtual Assistants(SVA) will equal the output of up to 140 million full-time workers by 2025.
How Smart Virtual Assistants are Supporting Assembly Line Workers
Let us see for example how smart virtual assistants support the assembly line in a car manufacturing plant.
Virtual assistants offload the burden of high-level tasks that may arise at every stage of the process, across functions, and around the clock, allowing humans to just handle decision-making. Virtual assistants have skyrocketed in popularity and have now become more customized, more context-aware and more conversational.
IoT and AI have transformed the automobile industry to the extent that in the future there is a possibility of one single robot controlling multitudes of robots to manufacturing a vehicle with near-zero human intervention. Cutting to the present scenario, the automobile industry is in a fusion state with a combination of humans, robots, AI/ML and IoT.
Smart virtual Assistants are gaining faster adoption in the assembly line due to their human-centered design methodology. As the virtual assistant (VA) is easily accessible, employees are capable of installing and using it to interact with the back-end systems for information inquiry without requiring a steep learning curve.
The other critical area is the data collected from the assembly line. Rather than depending on human labor to handle data-collecting activities, the VA takes an active part in issuing requests to relevant individuals when missing data is discovered. This will boost production and eliminate disruptions on the assembly line.
Generally, the assembly line for car manufacturing has to pass through 4 major steps or shops, viz., press shop, body shop, paint shop and the final assembly shop.
1. Handling floor queries
Workers and supervisors can query SVA on the details like temperature, torque, and vibration level of the machinery and fix the issues immediately. This quick look-up helps to avoid potential hazards or any delays in the production line. This also helps to break the information silos and helps the company to thrive with higher ROI.
Supervisors and managers can check the distribution of workload in different shops, check the production capability at a certain time, and know what kind of production and maintenance issues each shop is facing. It takes a lot of time to gather this information but with a chatbot, they will be able to get the information instantly. These AI-powered assistants will also become a crucial part of quality control by providing the manager with in-depth insights about procedures and the amount of attention they need.
2. Updates and delivery notifications
Assembly line employees will have to deal with a lot of information and data entry. With a chatbot, every employee can be notified and informed about updates. The chatbot will be able to give information about the production status, time and condition of the delivery, saving workers and the management team a lot of time to run around to see the production dashboards.
3. Improving operational efficiency
Virtual assistants when rightly integrated with internal systems can answer an endless number of questions without any hassle or waiting time. This availability makes operations and processes run smoothly while avoiding friction between Intra and inter-departments, which overall, directly affects production. With an SVA ready to take over standard and redundant tasks, the company finds itself with more resources human-wise and financially. Additionally, an SVA can keep track of various metrics by integrating them with existing systems ensuring optimal efficiency and providing escalation alerts when necessary. These alerts about key milestones and bottlenecks with the eventual ability to orchestrate on-the-fly changes that will resolve specific production problems.
Fortunately, conversational AI can manage many processes and interactions that require 24/7 support. Following are some of the examples
● Queries coming in high volumes
● Errors occurred due to manual processes
● Difficulties in managing bulk orders
● Facing issues in inventory planning
● Answering common employee FAQs
Offering employees with right information at the right time on the go can intensify their productivity and accelerate the production line.
4. Providing an interactive platform
Smart Assistants are an effective way of communicating because they do not deliver a passive experience to the user like emails, but rather an engaging interactive conversation that helps them with their queries instantly and makes them comfortable. It provides workers with instant access to controlled knowledge databases that will equip and enable them to perform their roles and responsibilities without any hassle. It acts as a communication bridge between management and employees. It provides instant alerts, notifications, responses on workloads, leave management, holiday, escalation, training needs, HR issues, etc.
5. Support Maintenance
When running a car manufacturing plant, accurate environmental conditions should be maintained. For instance, operational efficiency decreases in a paint shop drastically if environmental temperatures change even a little bit. By integrating all technology platforms, conversational AI assistants will trigger alerts on any abnormal conditions.
Virtual Assistants provide insights on different metrics to understand the potential bottlenecks, equipment failures, gaps in the production process, quality issues and can schedule predictive maintenance. Workers and managers can gain entire knowledge of plant conditions on their smartphones with conversational AI-enabled interactions.
6. Enhancing Safety
Handling the safety of the workforce is very critical for any company. Pulling out an instruction book or training manual or tapping a tablet for e-manual while working with machinery/equipment or complicated tasks is not safe. Workers at the assembly line can now go hands-free with voice enabled conversational AI or SVA’s to ask queries and clarifications and continue to do their work. This helps to quicken the production process without compromising on safety.
Apart from that, SVA can offer employee safety information to supervisors and workers to protect themselves from industrial hazards. These tasks also involve alerting employees to safety issues, preventing injuries, and limiting liability exposure.
Conclusion
Virtual assistants can also offer operators ease of access to critical machine status and environmental data, helping them work smarter and more efficiently. Experts anticipate that virtual assistants will eventually play an even larger role, from proactive alerting that can improve operations, prevent downtime, and ensure high-quality production to automating particular actions and tasks so that workers on the plant floor can concentrate on higher-value tasks.